La fibra de carbono en las carrocerías modernas
Por: José Manuel Aguilar
El desarrollo de nuevos materiales ha traído diferentes alternativas para los fabricantes de automóviles, que día a día sus exigencias son mayores para ofrecernos productos que convivan de mejor manera con el medio ambiente, reduciendo el consumo de gasolinas o de materiales reciclados.
En un principio se pensaba solo en metales entre ellos los aceros de alto límite elástico, pasando también por el aluminio, hoy como si estuviéramos siendo parte de la ciencia ficción se piensa en los materiales compuestos principal mente en la fibra de carbono.
¿Qué es la fibra de carbono?
La fibra de carbono es un material sintético, proviene de los hidrocarburos, específicamente es una fibra obtenida por tratamiento térmico del Poliacrilonitrilo (PAN) material basé de diferentes copolímeros entre ellos el acrílico, el ABS etc.
En particular, el PAN es una fibra de plástico formada por largas cadenas de moléculas de carbono, oxigeno, nitrógeno e hidrógeno en forma de escalera.
Cuando se calienta el PAN en correctas condiciones de temperatura en una atmosfera inerte, las cadenas de moléculas de carbono se juntan mientras los demás elementos se separan, los átomos de carbono del polímero cambian de distribución y forma una estructura estable de anillos fuertemente unidos que soportan los unos a los otros.
Mediante un nuevo calentamiento, los anillos se juntan en ‘listones’ de hexágonos de átomos de carbono muy flexibles, a diferencia del grafito, cuya estructura permanece plana.
La unión flexible de los listones evita que se deslicen, como pasa en la estructura plana del grafito, lo que resulta en un notable incremento en la resistencia del material.
Los hilos de PAN son trefilados en filamentos cinco veces más delgados que un cabello humano y están compuestos entre 92 y 100 por ciento de átomos de carbono, según sean las propiedades que se busquen.
En síntesis, la fibra de carbono se produce por la quema controlada del oxígeno, nitrógeno y otros elementos diferentes al carbono de la fibra precursora, dejando solo el carbono en el material.
Hasta este punto del proceso se obtiene el producto primario: los filamentos individuales de carbono, también llamados mechas, con un diámetro que oscila entre 5 y 8 micras (μm), que son trenzados entre sí en grupos de 5.000 y 12.000 mechas y se conocen con el nombre de roving.
También existen rovings pesados (Heavy Tow) que se componen de 120.000 a 400.000 filamentos.
Tejidos de fibra de carbono
Tejido Plano 3k
Peso: 200 gr/m2
Tamaño del Filamento: 3k
Espesor: 0,25 mm
Tejido Twill 3k
Peso: 193gr/m2
Espesor: 0,25mm
La fibra de carbono por sí sola no tiene utilidad; necesita de otros materiales, como las resinas y los endurecedores o catalizadores para formar un material compuesto, denominado >CFRP< (Plástico Reforzado con Fibra de Carbono).
Por tanto, los materiales compuestos son aquéllos formados por dos o más materiales distintos sin que se produzca reacción química entre ellos y utilizan en su fabricación fibras sintéticas unidas con resinas, que dan lugar a materiales de alta calidad con baja densidad, gran durabilidad y resistencia.
Dependiendo de las características que se pretendan de la función de la pieza o el elemento de la carrocería a fabricar, se decidirá:
- La cantidad de filamentos que compongan el hilo del entramado.
- El tipo de tejido, la dirección del entramado le dará las cualidades de resistencia.
- La resina, siendo la más común la epoxica, le dará la resistencia a los agentes externos, como los atmosféricos.
Proceso de fabricación
Para fabricar piezas de fibra de carbono se utilizan diferentes procesos; entre estos, se encuentra:
La proceso de moldeo por contacto a mano, que consiste en la fabricación de piezas de material compuesto haciendo uso de brochas y rodillos para favorecer la impregnación de las fibras de refuerzo con resinas termoestables de baja o media viscosidad.
El proceso de pultrusión es la fabricación continúa, de bajo coste, automático y de alto volumen.
Las fibras impregnadas con resina son traccionadas a velocidad constante, a fin de obtener un producto de una sección prediseñada.
La infusión consiste en la fabricación de piezas de materiales compuestos, haciendo uso del vacío para favorecer la impregnación de las fibras de refuerzo con resinas termoestables de baja viscosidad.
Los materiales preimpregnados son semiproductos listos para su empleo y destinados a la producción de grandes series.
Consisten en un proceso manual que emplea láminas de fibra de carbono en cualquier presentación de las mencionadas anteriormente.
Están impregnadas en resina reactiva en estado inicial de polimerización (termoendurecible) y precisan de un procesado final para su completa polimerización; normalmente, mediante calor (140º) se obtiene el producto termoendurecible.
Por último, uno de los procesos más utilizados en fabricación con estos materiales compuestos, consiste en la utilización de estructuras tipo sándwich, que forman un núcleo y dos recubrimientos, que actúan como una unidad, debido a que están pegados.
El núcleo puede ser de aramida o aluminio, tipo celdilla de abeja, madera de balsa, >PVC<, corcho, etc., y los dos recubrimientos monolíticos, de fibra de carbono.
Propiedades de la fibra de carbono
- Alta resistencia mecánica.
- Peso ligero.
- Excelente tenacidad.
- Resistencia a la corrosión y al envejecimiento.
- Buenas propiedades antiestáticas.
- Alta resistencia al impacto.
- Muy buenas propiedades dieléctricas.
- Alta resistencia a los ácidos, alcalinos y algunos disolventes.
- Alto módulo de elasticidad.
- Baja densidad, 4.5 veces menor que el acero.
- Buena propiedad ignifuga.
- Resistencia a la fatiga.
- Gran flexibilidad, etc.
Utilidad en el automóvil
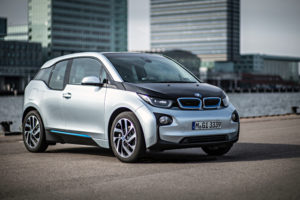
El BMW i3 cuenta con piezas de fibra de carbono.
La cuna de la fibra de carbono en el automóvil ha sido la Fórmula 1 para, paulatinamente, incorporarse al resto de vehículos, llegando no solamente a los deportivos sino también a todos los modelos de las diferentes gamas, vehículos industriales, motocicletas y bicicletas.
El objetivo principal al utilizar este material es conseguir vehículos que pesen un 40 por ciento menos.
Uno de los principales constructores en dar el primer paso ha sido BMW, que ha incorporado piezas de fibra de carbono en un gran número de vehículos y ha fabricado vehículos eléctricos con la carrocería totalmente de fibra de carbono.
BMW Group, junto con SGL (Automotive Carbon Fibers), en septiembre de 2011, inauguraron una planta de producción de fibra de carbono para producir piezas y carrocerías a gran escala, en 2013. El primer vehículo en usar la fibra de carbono de esta planta es el BMW-i3, totalmente eléctrico; emplea la tecnología Life-Drive.
El módulo inferior o Drive, incluye una plataforma de aluminio, el motor eléctrico y las baterías, que van alojadas debajo del piso.
El Life, o módulo de supervivencia, es el compartimento de pasajeros fabricado con plásticos reforzados con fibra de carbono ultraligera.
El uso de este material en todo el vehículo le aporta una gran ligereza que le ayuda a mejorar la autonomía, las prestaciones finales y la resistencia estructural.
Nissan apuesta por materiales ligeros como la fibra de carbono para sus vehículos eléctricos.
Los materiales compuestos reforzados con fibra de carbono, son el fruto de las nuevas tecnologías de fabricación, que brinda grandes ventajas para un mejor desempeño de los automóviles en el ahorro de combustibles, prestaciones dinámicas y aerodinámicas como se ha comprobado en la Formula 1, ahora en el presente estas tecnologías ya se emplean en la fabricación de vehículos de serie, lo que representa un motivo más para estar actualizados en los nuevos procesos de reparación.
Por lo que cada vez el técnico de un taller de carrocería tendrá nuevos retos, los que generarán un mayor profesionalismo en el sector.